LOOK AT IT!
What a week. Do I say that every week?
Monday! WELL, I got most of that water pump bolt out. I also damaged the old thread… alas. I ordered a thread repair kit then headed to Wickes for a sheet of aluminium for the vents, and a PVC pipe for the water tank inlet.
The kit arrived on Tuesday and, slight tangent, but it included an advert for a model engineering exhibition in Leamington Spa. Now the company, Tracy Tools, is based in Torquay, about two hundred miles away! They didn’t have to do that, but somebody saw the address and thought “You know, this fella might be interested in model engineering” and guess what? I might just go. God I love personalised advertising. (It could all be coincidence, or it’s automated, or they put the same one in every package, but I choose to believe.)
That evening I got to work fixing the thread: drilling a slightly larger hole in the engine block, threading that and then inserting the repair thread (a “Heli-Coil”)… fingers crossed. The day before I also increased the size of the holes in the water pump itself, as they didn’t quite line up with the ones in the engine block. I’d gone to the chandlery asking why, why is the water pump you sold me a misfit?!, and I got a history lesson: when BMC was sold (to a company in Turkey I think? Then India…), it did not include the castings. So they had to make new ones for the engine parts, and said new ones do not quite match the old, as in my case.
Anyway, larger holes, thread re-tapped… it was time to install this darned pump. I jimmied up the bolts with copper grease, got it all in place and starting torquing them, correctly this time. Well, almost: the manual said 24Nm, the lowest setting on the torque wrench was 28. The other 3 clicked fine, but I couldn’t quite get this repaired thread there; it kept slipping at what I guess was about 20Nm. Still, it felt tight, and the others were slightly over spec. Cautiously optimistic, I celebrated. THE WATER PUMP WAS BACK ON. Given that I’ve never seen this thread, or the mess I made, or the repair I’ve attempted, this was a biblical win.
I could now assemble the rest of the engine, but it was getting dark so I settled for some electroplating instead. Part of the shoot bolts I made for the door were regular ol’ mild steel, and although they wouldn’t see much weather, paint would scuff and I wanted something to protect them from rust: a coat of zinc. I bought some zinc sheets and sulphate powder online, and with a little battery set up a science project:
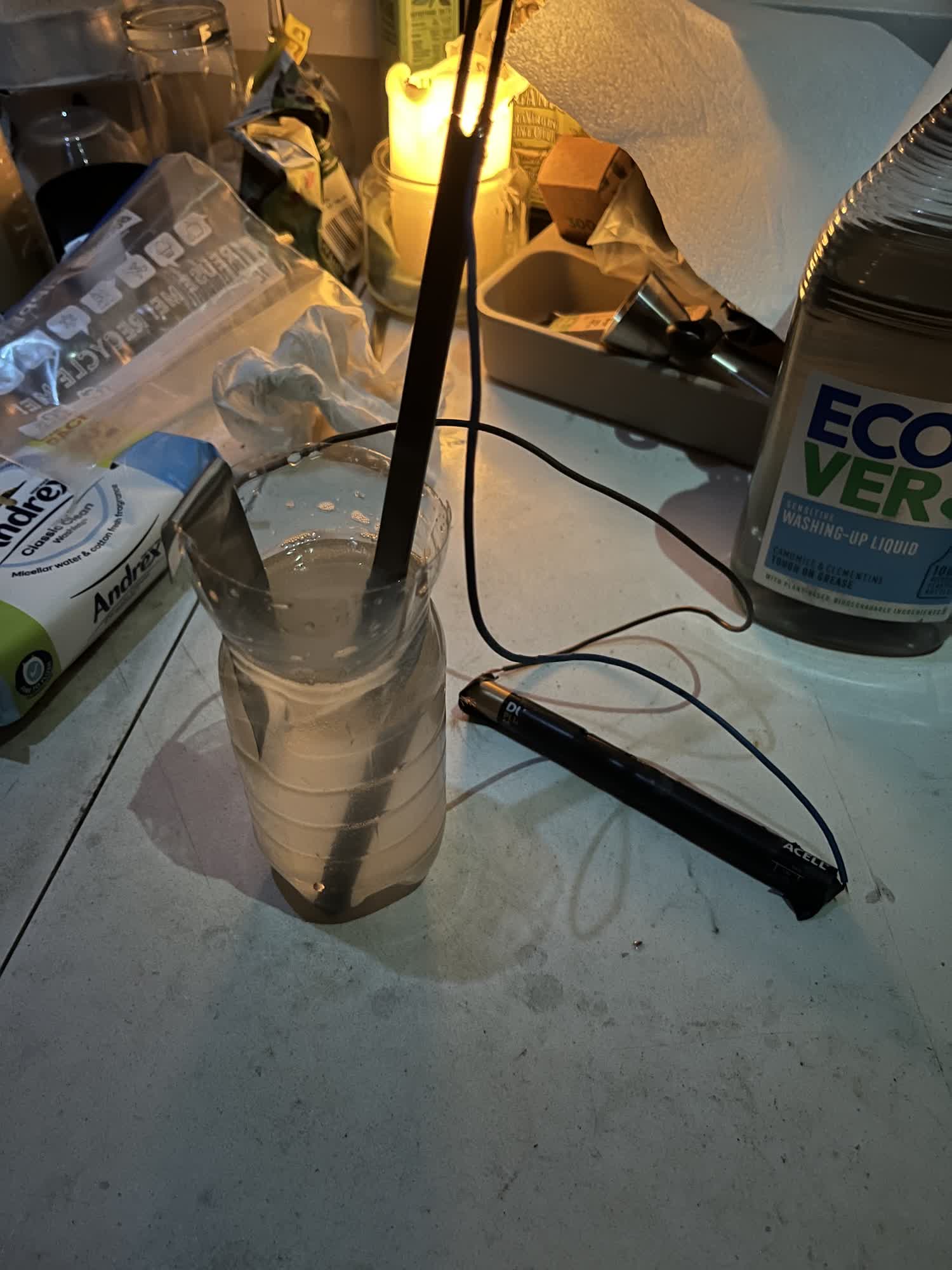
90g of the powder dissolved in 300g of water, 3 AA batteries in series with the positive terminal connected to a sheet of zinc in the water, the negative attached to the bolt for galvanising, and a minute or so later and it was done! I was expecting bubbles, but that could be to do with the low current or my bodge of a clean (you’re “supposed” to use an acid). Unfortunately I forgot to take a photo of the finished product, and it’s now hidden it the door, but you may take my word that the steel looked different, and it certainly tasted of zinc.
On Wednesday I cut the latch and bolt holes in the other door, and locked the door for the first time since June! But… I drilled some holes slightly too small, so had to take the handle with me:
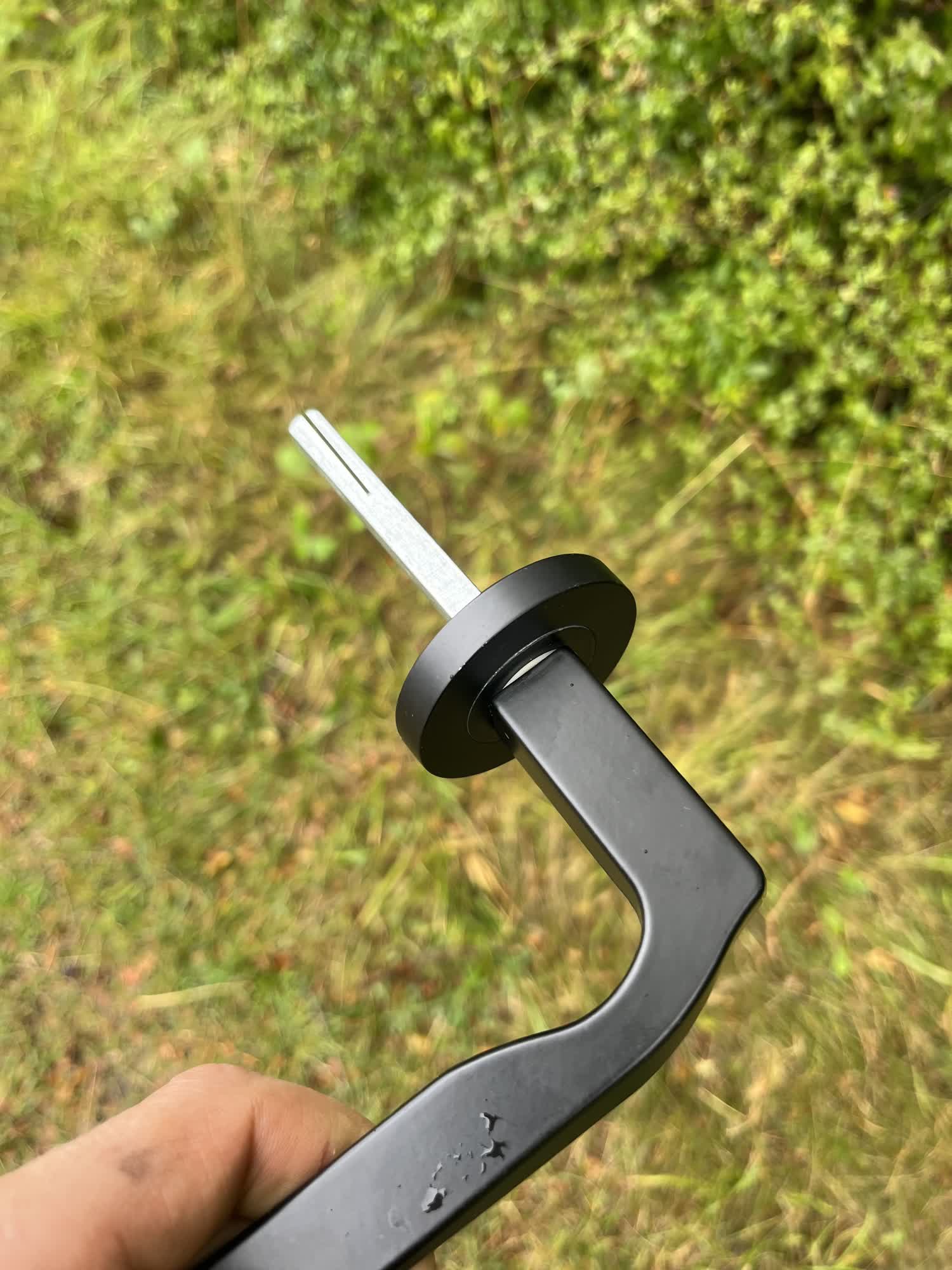
The next few days were engine assembly; I was nervously hyped. It was one of the harder Mechano sets I’ve played with, as whoever took it apart didn’t quite label all the nuts and bolts and where they belonged. But with some deduction and guesswork the pieces did come together, and it was so satisfying to clear the boat floor of parts. It was looking like an engine again:
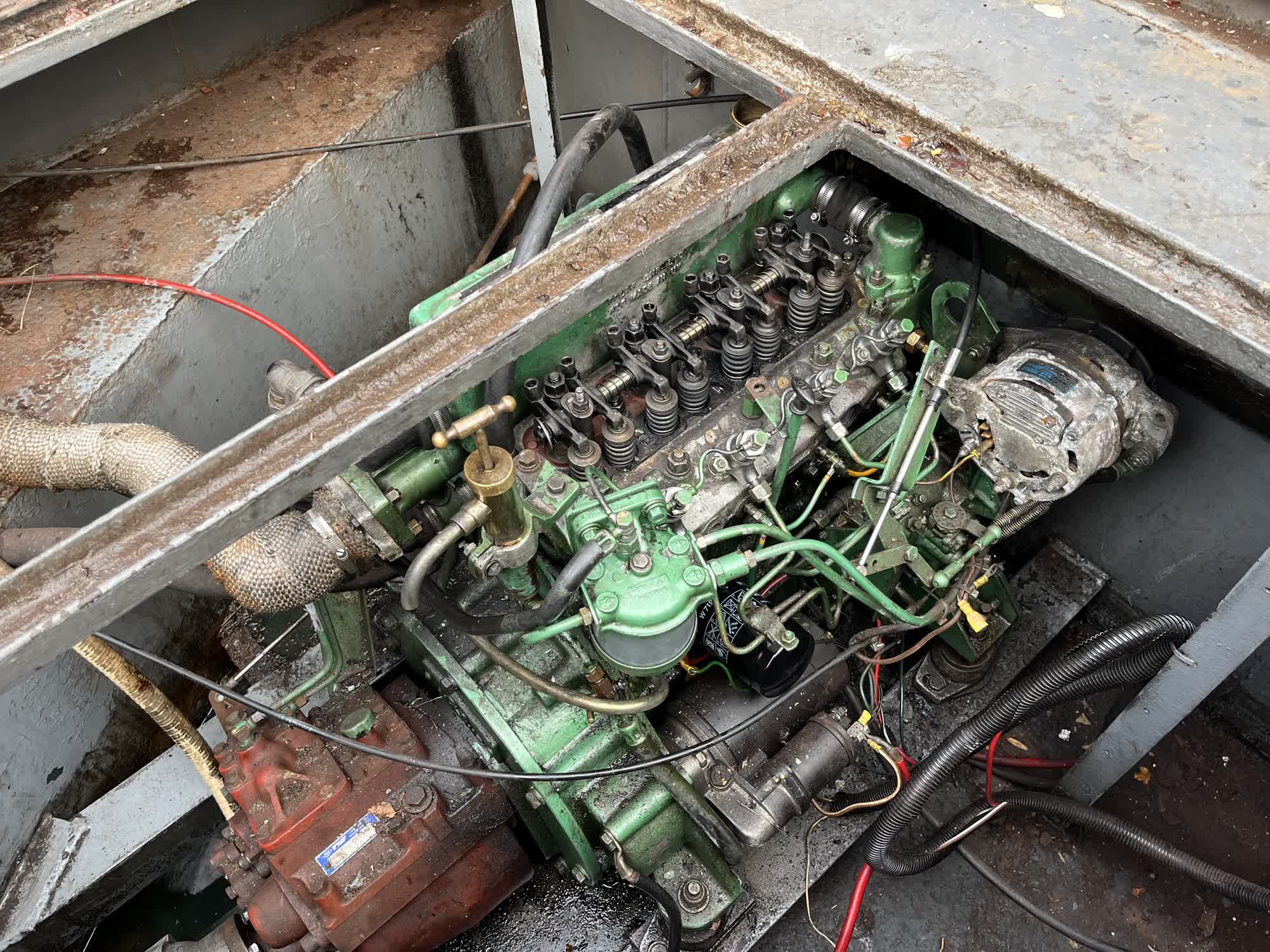
First thing on Friday was to torque the cylinder head: 14 nuts needed 102Nm, and done in a specific order (roughly from the centre outwards.) Now 3 of the nuts were inaccessible with the wrench, sat under the rocker (you can just about see them above!), and there is a special tool you can get but I wasn’t going to wait, so those underwent a “vibes-based” process, and let me tell you: the vibes were good.
Saturday was le big day. First thing: tappets, or the rocker valve clearances, set to 14 thousandths of an inch. I went to pick up some feeler gauges to check those, after which I put the alternator belt back on and topped up the oil. It was time. I heated the glow plugs for about 20 seconds and cranked the engine, and it spluttered to life with a puff of white smoke! For all of 5 seconds…
It then wheezed and wouldn’t start, but with a little guidance I was prompted to check the fuel, which I had indeed not bled correctly… simple, really: no diesel, no power.
Some pumping later to bleed the fuel regulator and each injector, and after doing the 3rd one it came to life! It wouldn’t idle though, so I lightly held the throttle for 5 minutes after which it started to smooth out. 20 minutes later it was still going, and starting to sound wonderful. I couldn’t quite believe it, a mix of joy and euphoria and hysterical disbelief, it worked:
LOOK AT IT!
I turned it off and let it rest for an hour while I went to B&Q to pick up wood for the rest of the battens, and back at the boat it started right away. A few minutes of idling and off I went, a whole 200m to where I could moor the boat next to the van for errands: trash was piling up, and I was out of water. It felt good to move again:
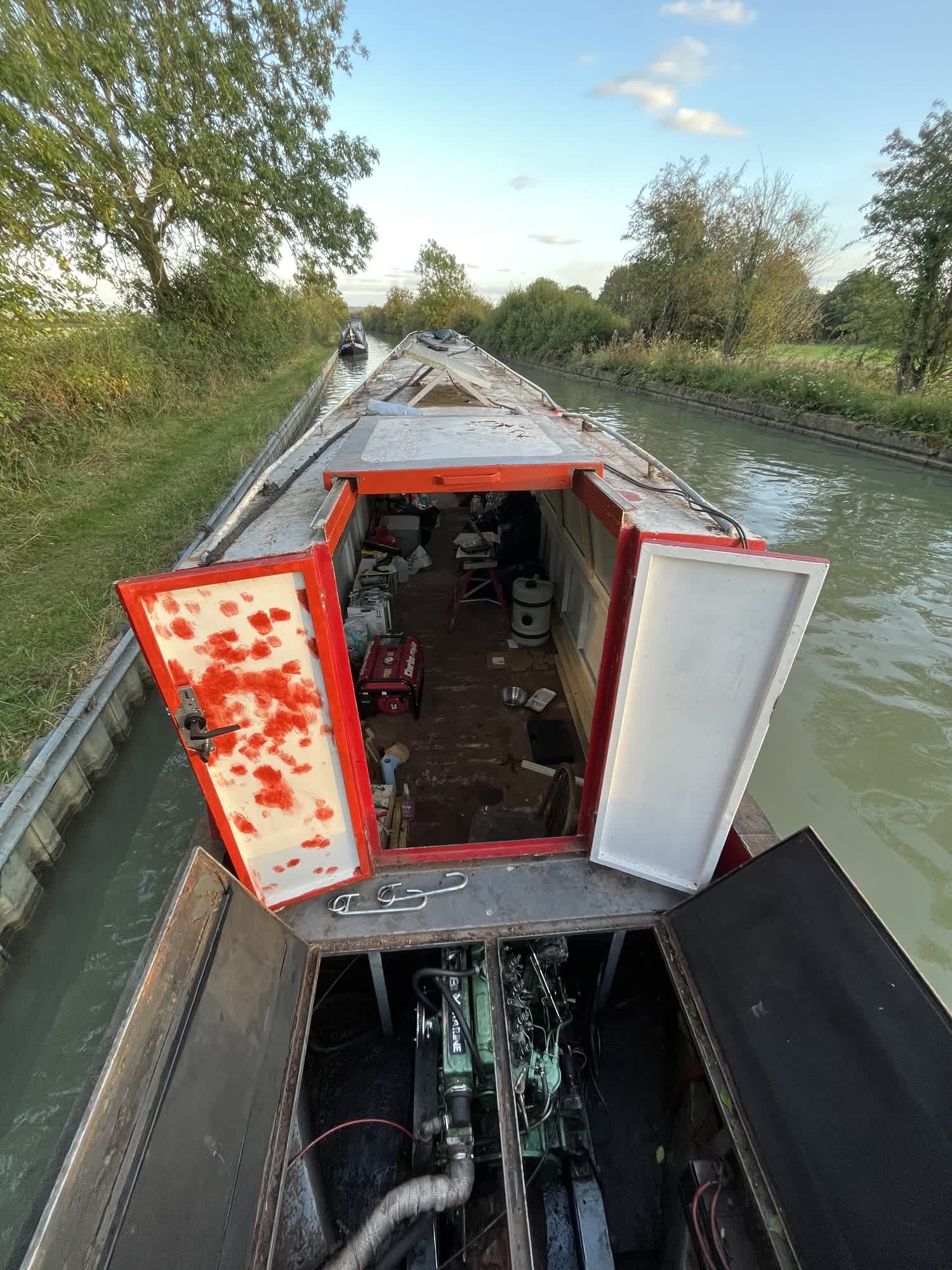
It’s not quite over yet, though: in the next few days I’ll run it again and re-torque the cylinder head nuts, along with re-checking the valve clearances.
But I couldn’t stop, wouldn’t stop: good weather was looming, and days to insulate were running out. Sunday — today! — has been all-out battening, and with help from some Danish dynamite half of the boat is ready for foam (photo taken before finishing):
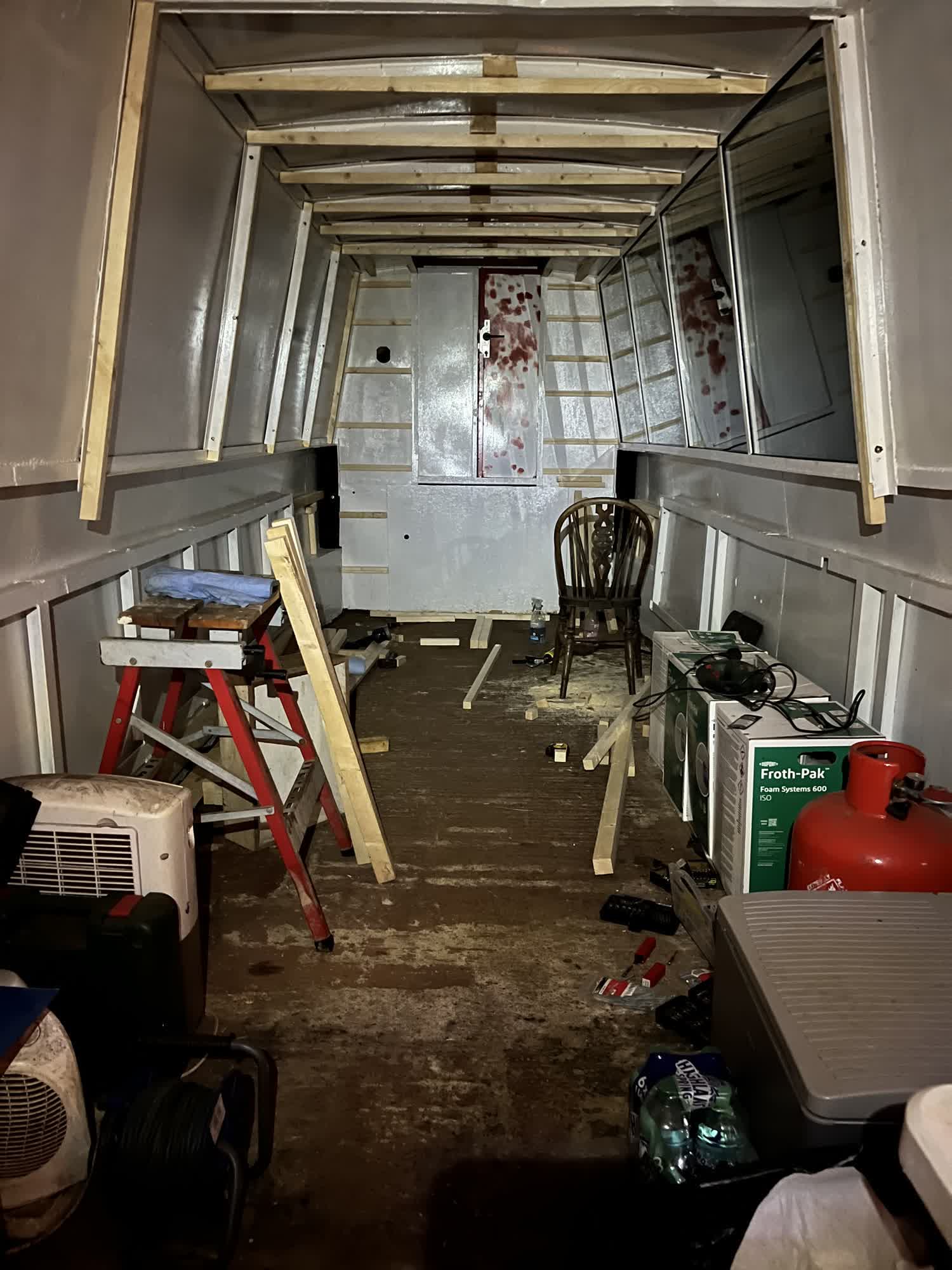
It’s coming together.
Until next Sunday!
- Nick